Today’s food industry faces numerous challenges related to maintaining high product quality and minimizing production waste. Traditional quality control methods are often time-consuming and prone to human error, leading to inefficiencies and increased costs. In this article, we present a hypothetical case study illustrating how an advanced image detection system can revolutionize quality control in the food industry, using a large fruit and vegetable processing company as an example.
Problem Description and Project Objective
The company specializes in producing jams, juices, canned vegetables, and frozen foods. It processes thousands of tons of raw materials daily on its extensive production lines. The main challenge for the company is maintaining high product quality, minimizing waste, and quickly identifying production defects, such as contamination, mechanical damage to fruits and vegetables, and non-compliance with quality standards. Traditional quality control methods proved inadequate, prompting the company to implement an AI-based automated image detection system.
The project’s goal was to develop and implement an advanced AI system that would automatically inspect food products on the production line, identifying defects and damage. The system aimed to increase quality control efficiency by automating the process, reduce production waste by quickly detecting defects, and improve the overall quality of products delivered to the market, leading to higher customer satisfaction.
Data Preparation
Three months prior to the project, the company installed cameras at key stages of the production line. Cameras were installed at the raw material intake, over sorting lines, and at packaging machines. These strategic locations allowed monitoring the quality of raw materials and products at various production stages. The cameras captured images of raw materials such as apples, tomatoes, peppers, carrots, and potatoes, which were then analyzed for defects and damage.
Over three months, the company collected about 500,000 image records, with a daily increase of about 5,000 new images. This data was stored on local servers and in the cloud, ensuring easy access to large datasets. Each record included a timestamp, location on the production line, product type, and a description of the defect if detected. During data collection, some camera methods and locations were modified to improve the quality of the collected data. Missing data was supplemented by additional photo sessions and camera configuration improvements.
Model Selection and Training
Advanced AI technologies and tools such as Pytorch and OpenCV were used for system implementation. Convolutional Neural Networks (CNNs) were chosen for their effectiveness in image analysis tasks, thanks to their ability to automatically detect features and patterns. Transfer learning was also utilized, using the pre-trained YOLO model, which was adapted to the specific data of the food industry.
The image data was preprocessed using OpenCV, including color correction, lighting normalization, and noise removal. Data augmentation, such as rotation, scaling, and changes in brightness and contrast, was applied to increase the training dataset and improve model generalization. CNN models were trained on large image datasets, covering different classes of raw materials and various types of defects. The training process was accelerated using GPUs with NVIDIA CUDA technology, allowing efficient processing of large datasets.
Implementation and Integration
The image detection model was deployed on AWS servers with GPU support to ensure fast image data processing. AWS EC2 servers with p3.2xlarge instances were used for scaling and system performance. A RESTful API was created using Flask, enabling communication between the image detection system and the production line. The API handled HTTP POST requests for sending images and receiving analysis results.
The API was integrated with the company’s existing production system, enabling automatic image transfer from cameras to the image detection system. The production system sent images to the API in real-time, and analysis results were returned to the production system for appropriate actions, such as removing defective products from the line.
Monitoring and management tools, such as Amazon CloudWatch, were implemented to ensure continuous system availability and performance.
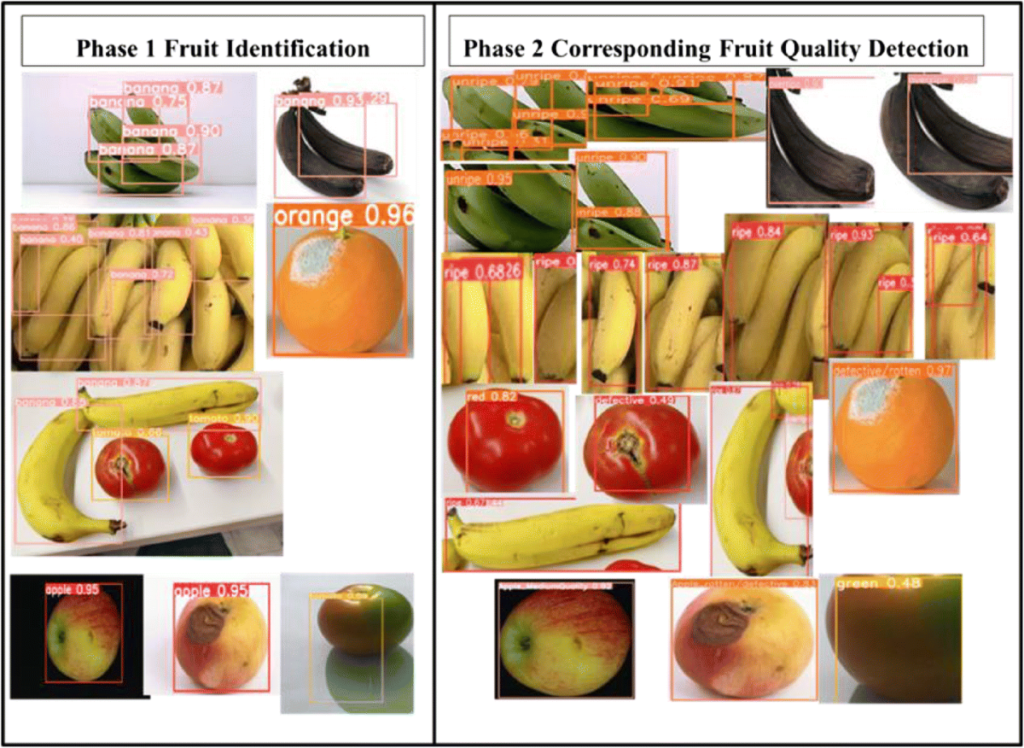
Results Achieved
The system achieved 80% accuracy in detecting raw material defects, resulting in significant business benefits for the producer. The implementation reduced production waste by 20%, equivalent to 10 tons less waste per month.
The efficiency of raw material quality control increased by 50%, leading to faster and more accurate inspections. Assuming the cost of labor associated with raw material quality control is 50,000 PLN per month, the savings from increased efficiency amounted to 25,000 PLN per month.
Costs and Resources
The project involved three Data Scientists and a part-time Project Manager, lasting 4 months, covering data preparation, model training, and system deployment.
AWS servers were used for model training and image detection system deployment. Model training on EC2 p3.2xlarge instances cost 10,600 PLN for 900 hours of work. Deployment and operations on EC2 t3.large instances cost 900 PLN for 4 months of work. Data storage on Amazon S3 cost 700 PLN for 2 TB of data over 4 months, and using Amazon RDS for database storage cost 1,100 PLN.
The total project cost amounted to 513,300 PLN.
Monitoring and Optimization
The system was monitored for availability and performance using Amazon CloudWatch, and the image detection models were regularly updated monthly to account for changes in raw materials and new defect types. An alert system informed the team of any irregularities, such as performance drops or data availability issues.
Interaction with the Technical Team
Collaboration between teams was crucial for the project’s success. Regular meetings were held between the data science, IT, production, and quality management teams to discuss project progress, exchange ideas, and identify potential issues. All project stages were thoroughly documented, including technical specifications, data analysis reports, A/B test results, and recommendations for further actions. Training was conducted for the production team on using the image detection system and interpreting the results to maximize the tool’s potential.
Challenges and Future Directions
The project faced several challenges, such as ensuring system scalability to handle increasing amounts of data and raw materials, and continuously improving detection model accuracy through regular updates and algorithm optimization. Integration with various production systems and ensuring compatibility also posed challenges.
In the future, the food producer plans to expand the detection scope, introducing the detection of other defect types, such as structural deformations or color changes. Increasing automation through more advanced decision-making mechanisms on the production line and utilizing advanced analytics for predicting quality issues and optimizing production processes are the next steps in system development.
Summary
The implementation of an advanced image detection system brought significant benefits, such as reducing production waste, increasing the efficiency of raw material quality control, and improving product quality. Although the project faced some challenges, the business benefits of implementing the system were substantial, and the company plans further development and optimization of the system in the future.
This hypothetical case study shows how artificial intelligence can revolutionize the food industry, bringing tangible benefits to both producers and consumers.
Interested in a similar solution? Contact us.